فهرست مطالب
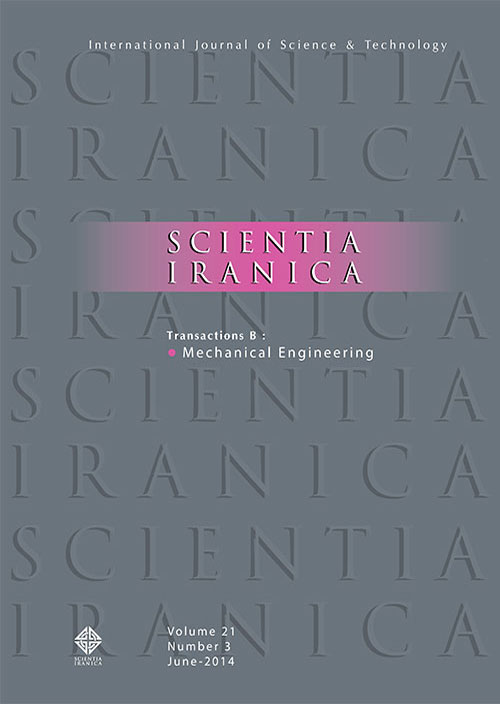
Scientia Iranica
Volume:27 Issue: 6, Nov-Dec 2020
- (Transactions on Industrial Engineering (E
- تاریخ انتشار: 1399/10/14
- تعداد عناوین: 9
-
-
Pages 3219-3232
Many works published in the area of cellular manufacturing system are based on the assumption that machines are reliable in the whole production horizon without any break down. As such assumptions often are not realistic, to contribute to closing this gap to reality, the model has been modified by additionally including machine reliability, alternative process routings and workforce assignment in a dynamic environment. In this research to integrate this aspects, the modified problem has been defined and formulated and an extended mixed integer multi-period mathematical model has been proposed. In order to evaluate the effectiveness and capability of the extended model, some hypothetical numerical instances are generated and computational experiment are carried out using Gams optimization package. Experimental results demonstrate that the demand value can affect the machine breakdown rate, and a machine with a minimum breakdown rate is implemented more often than others. Moreover, the observed trade-off between the workforce-related costs and the cell-formation costs indicates that workforce-related issues have a significant impact on the total efficiency of the system. The proposed model can be implemented in medium- and large-scale manufacturing companies.
Keywords: multi-period cellular manufacturing system, machine reliability, workforce learning-forgetting effect, alternative process routing -
Pages 3233-3241
Using multivariate control chart instead of establishing univariate control chart for all variables in processes provides time and labor advantage. In addition, it is considered in the relations between variables. However, the statistical calculation of the measured values of all variables is seen as a single value in the control chart. Therefore, it is necessary to determine which variable(s) is the cause of the out of control signal. Effective corrective measures can only be developed when the causes of the fault(s) are determined correctly. The aim of the study is to determine the machine learning techniques that will accurately estimate the type of fault. With the Hotelling T2 chart, out of control signals are identified and the types of faults affected by the variables are defined. Various machine learning techniques are used to compare classification performances. The developed model was applied in the evaluation of the paint quality in a painting process. ANN was determined as the most successful techniques according to performance criteria. The novelty of the study is to classify the fault according to the types of faults, not the variables. Defining the faults according to its types will enable to take effective corrective actions quickly.
Keywords: Multivariate controlchart, Naive Bayes-kernel, K-nearest neighbor, Decision tree, Arti cial neuralnetworks, Multi-layerperceptron, Deep learning -
Pages 3242-3252
In this study, we propose a method to determine the weight of decision makers (DMs) in group multiple criteria decision making (GMCDM) problems with interval data .Here, we obtain an interval weight for each DM and the relative closeness of each decision from the negative ideal solution (NIS) and the positive ideal solution (PIS) is then computed. In the proposed method, after weighting the decision matrix of each DM, the alternatives are ranked using interval arithmetic. A comparative example together with a real world problem on air quality assessment is given to illustrate our method. Our findings show that the proposed approach is a suitable tool to solve GMCDM problems.
Keywords: Decision Analysis, GMCDM, TOPSIS, interval matrix, weight of criteria -
Pages 3253-3264
This paper generalizes the standard economic production quantity (EPQ) model in process manufacturing industry by incorporating regular preventive maintenance (PM) activities into classic EPQ model. The PM program improves the condition of the production to an acceptable level, and avoids potential stoppages and disruptions, hence, it is a vital task in every production process. However, the standard EPQ model does not consider PM activities and then is not applicable to real-world situations. We consider manufacturer which produces a product under EPQ setting with a defective production process, in which every production cycle involves a number of sub-production cycles. Two models are proposed, based on the disposal time of defective items, to determine optimal number of sub-production cycles. In model I, the disposal of defective items is performed once per cycle at the end of each production cycle, while in model II, the disposal of defective items is performed multiple times per cycle, at the end of each sub-production cycle. The total cost functions are derived for each model separately, and then simple solution algorithms are designed. A numerical example is presented and discussed to evaluate proposed models. The results illustrate that model II is more cost effective than model I.
Keywords: Preventivemaintenance, Production-inventorysystem, Defective process, Manufacturingplanning, Defective items -
Pages 3265-3288
In the modern industrial environment, there is a continuous need for the advancement and improvement of the organization’s operations. Learning is an inherent property which is time-dependent and comes with experience. In view of this, the present framework considers the process of learning for an imperfect production system which aids in reducing the setup cost with the level of maturity gained, hence, providing positive results for the organization. Because of machine disturbances/ malfunctions, defectives are manufactured with a known probability density function. To satisfy the demand with good products only, the manufacturer invests in a two-way inspection process with multiple screening constraints. The first inspection misclassifies some of the items and delivers inaccuracies, viz., Type-I and Type–II. The loss due to inspection at the first stage is managed efficiently through a second inspection which is presumed to be free from errors. The study mutually optimizes the production and backordering quantities in order to maximize the expected total profit per unit time. Numerical analysis and detailed sensitivity analysis is carried out to validate the hypothesis and further cater to some valuable implications.
Keywords: Inventory, Imperfect-production, Two-way inspection, Sales-returns, Learning, Screening-constraints -
Pages 3289-3304
This paper combines the newsboy problem with the cooperative advertisement problem in the presence of uncertain demand which depends on retail price as well as both local and national advertising expenditures to coordinate pricing, ordering, and advertising decisions in a manufacturer-retailer supply chain. A game theoretic approach is adopted to determine the equilibrium values of the decisions. Three different game scenarios based on the newsboy problem model are developed and analyzed: 1) Stackelberg manufacturer game in which manufacturer as the dominant power plays the role of leader in the market and the follower retailer makes its own best decisions after observing the leader decisions, 2) Nash game wherein both manufacturer and retailer have equal power in the market and make their decisions simultaneously to find their own best strategies and 3) centralized scenario in which retailer and manufacturer make the best decisions by information sharing and joint cooperation. The equilibrium decisions are obtained exactly in the three scenarios. Some corollaries are also presented and theoretically proved to show the relationships among the variables in centralized vs. decentralized supply chain. Finally, some numerical examples are randomly generated and a sensitivity analysis is carried out to show capabilities of the proposed models.
Keywords: Supply chaincoordination, Newsboy problem, Pricing, Cooperativeadvertising, Ordering, Uncertainty, Game theory -
Pages 3305-3321
Recently, design of preventive maintenance (PM) policies during the warranty period has attracted the attention of researchers. The methods mainly design warranty servicing strategies in a way that reduce the cost imposed on the manufacturer without considering the impact of customer dissatisfaction. While dissatisfaction with a product is an important issue which may result in the loss of potential buyers and switching existing buyers to competitors. Therefore, this study develops a bi-objective model which simultaneously minimizes the manufacturer and the buyer cost under a Non-homogeneous Poisson Process framework. Also, a non-periodic preventive maintenance strategy is presented in which PM actions are performed at discrete time instants in a way that the expected number of failures remains a constant value over all PM intervals. Furthermore, it is a known fact that the value of money reduces over time due to different reasons and has a significant impact on long-term contracts. Since PMs and repairs are conducted at different times, the time value of money is considered to estimate the cost more accurately. A comparative study is conducted to support this claim that the presented non-periodic reliability-based PM policy has a better performance in comparison with a periodic PM policy.
Keywords: Warranty, Non-periodicpreventivemaintenance, Time value of money, Bi-objectiveoptimization -
Pages 3322-3337
Technology valuation, especially in the early stages of new technology-based firms (NTBFs) growth is one of the most critical challenges, which most often hinders the investor and entrepreneur's deals during the venture capital (VC) financing process. It is clear that uncertainties arising from the likelihood of implementing public policies could significantly affect the volatility of NTBFs cash flows in the field of cleaner production. Commonly, these kinds of technologies require public supportive policies for achieving success. Consequently, their technology valuation is more challenging and traditional valuation methods are not suitable anymore because of the definitive assumption of cash flow and ignoring the investors’ flexibilities and uncertainties. Therefore, this paper proposes a method by introducing a framework based on the decision tree and the real options analysis which is tailored to meet the technology valuation of such firms during all stages of their growth. Furthermore, unlike previous papers that have utilized the compound options, option to choose has been used to apply investors’ flexibilities. Then, the proposed framework is supported by a case study, which has been conducted to verify and validate it. Finally, the conclusion section discusses the contributions and limitations of the study and provides directions for future research.
Keywords: Technology valuation, New technology-based rms (NTBFs), Real Options Analysis(ROA), Option to choose, Decision Tree Analysis(DTA), Cleaner production -
Pages 3338-3351
The inventory model for deteriorating items, which is developed by The Evidential Reasoning Algorithm (ERA) and the imprecise inventory costs, is one of the most important factors in complex systems which plays a vital role in Payment. The ERA is able to strengthen the precision of the model and give the perfect interval-valued utility. In this model, during lead-time and reorder level two different cases can be happened which the mathematical model turns into an imposed nonlinear mixed integer problem with interval objective for each case. Placement of an order, which is overlooked by many researchers till now, is normally connected with the advance payment (AP) in business. Specifying the optimal profit and the optimal number of cycles in the finite time horizon and lot-sizing in each cycle, are our goals so. In order to solve this model, we apply the real-coded genetic algorithm (RCGA) with ranking selection. By the model, we represent some numerical examples and also a sensitivity analysis with the variation of different inventory parameters.
Keywords: Evidence theory, Inventory, Advance payment, Deterioration, Genetic algorithm, Interval orderrelation